Double injection, also known as two-shot or dual-shot injection molding, is an advanced manufacturing process used to produce complex plastic parts with two different materials or colors. This process allows for the creation of parts that have multiple components or features in a single production step, reducing the need for additional assembly processes.
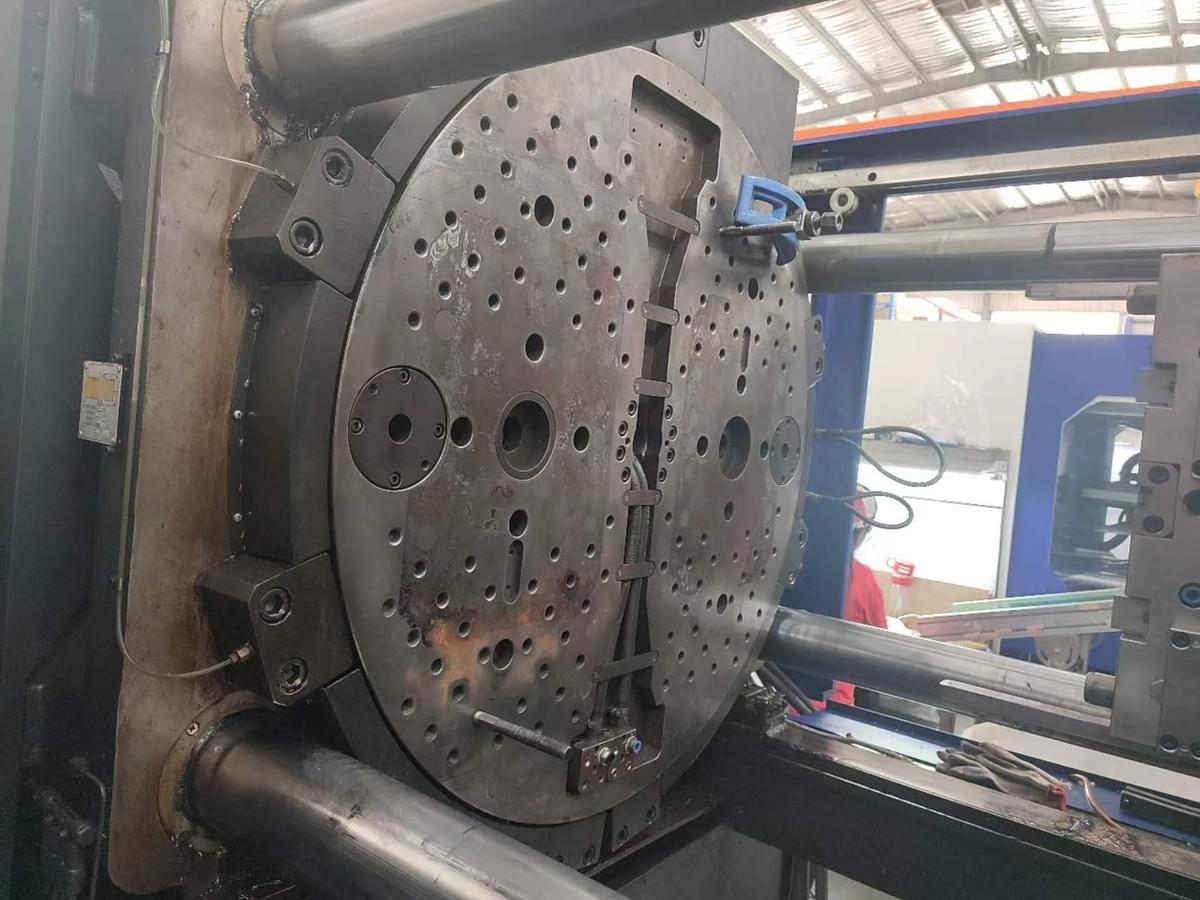
The double injection molding process involves the following steps:
Injection of the First Material:
The first step is to inject the first material into the mold cavity using the first injection unit of the molding machine. This material forms the initial part of the component.
Mold Rotation or Indexing:
After the first material is injected and partially fills the mold cavity, the mold is rotated or indexed to a different position to prepare for the second injection.
Injection of the Second Material:
The second injection unit, which contains a different material or color, then injects the second material into the same mold cavity. This material bonds with the first material to create a seamless interface between the two components.
Cooling and Solidification:
Once both materials are injected, the mold is cooled to allow the materials to solidify and take the desired shape.
Ejection and Finishing:
After the part has solidified, it is ejected from the mold, and any additional finishing processes, such as trimming or assembly, may be performed.
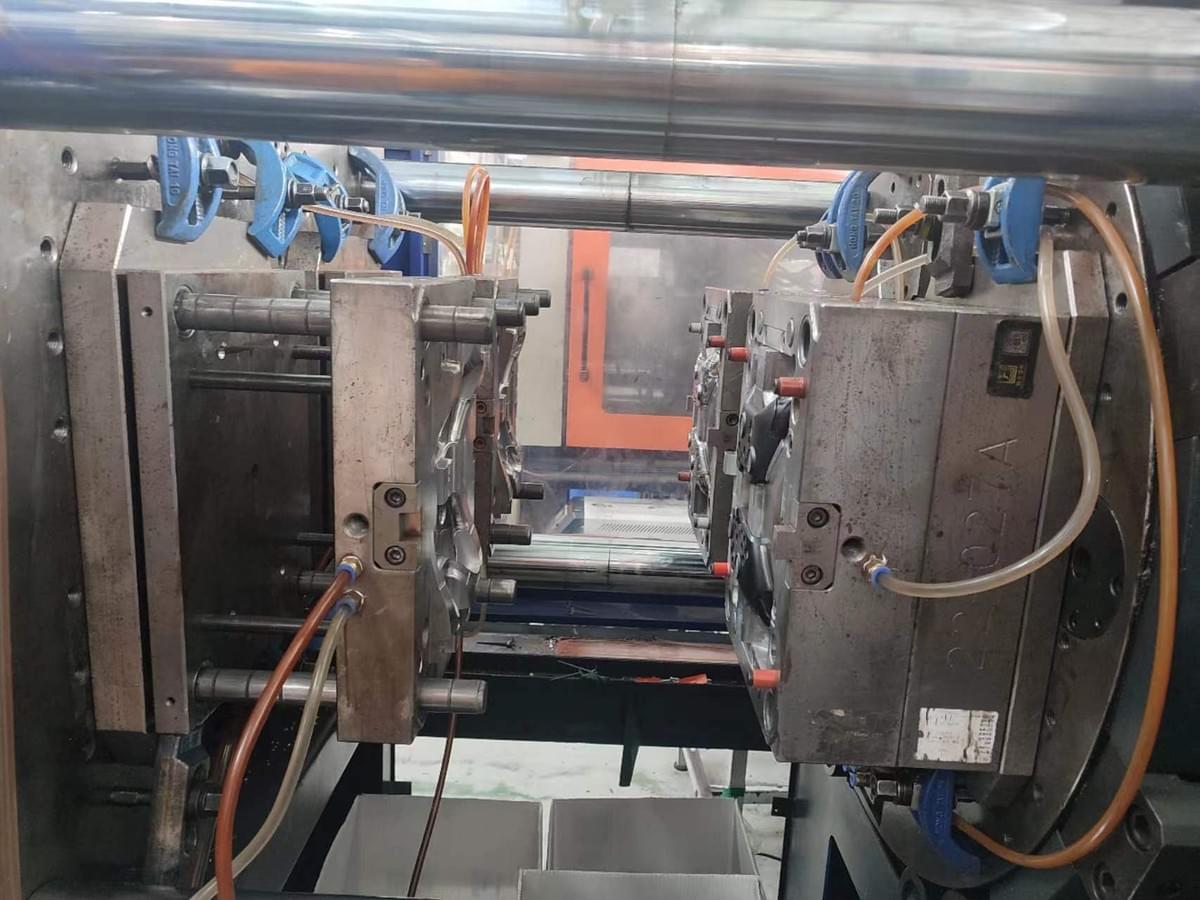
Double injection molding offers several advantages:
Enhanced Design Capabilities: The process allows for the creation of complex, multi-material or multi-colored parts with intricate geometries that would be challenging or impossible to achieve with conventional molding techniques.
Reduced Assembly Costs: Since the two materials are combined in a single mold, there is no need for separate assembly steps, leading to cost savings and improved production efficiency.
Improved Product Functionality: Dual-shot molding enables the integration of different materials with varying properties in a single part, enhancing the overall functionality and performance of the component.
Enhanced Aesthetics: By using different colors or materials, manufacturers can achieve visually appealing and attractive designs without the need for painting or additional surface treatments.
Double injection molding is commonly used in industries such as automotive, electronics, consumer goods, and medical devices, where there is a demand for complex parts with multiple functionalities or aesthetic requirements. It is a versatile and efficient manufacturing process that continues to find applications in various industries.